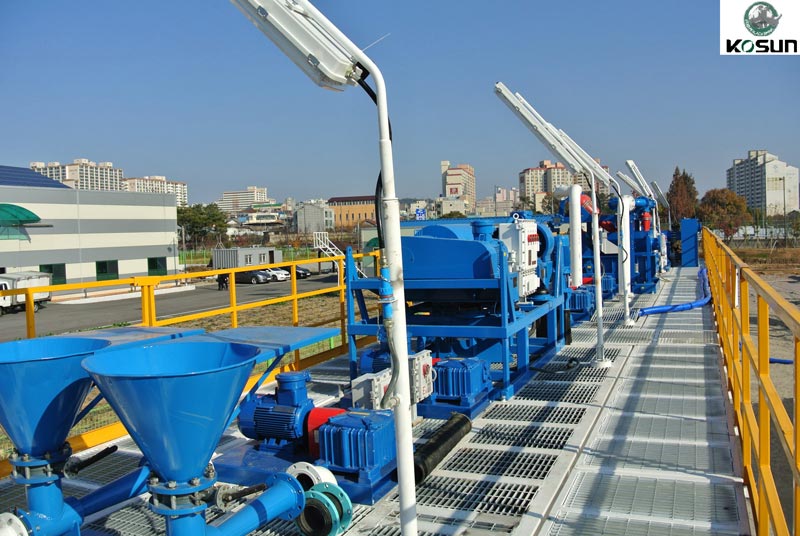
Система контроля примесей бурового раствора южнокорейской буровой установки для бурения скважин на воду
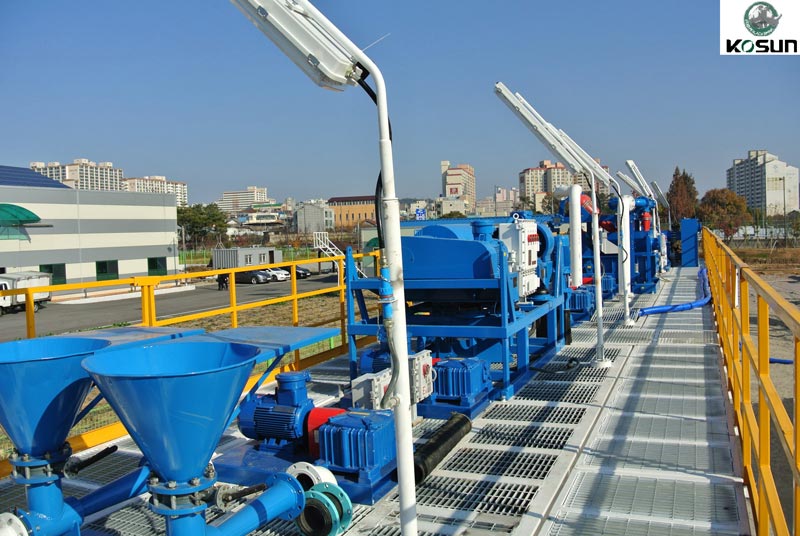
Циркуляционной системы буровой установки KOSUN
Циркуляционная система буровых установок включает в себя (Вибросито,Центрифуга, Газосепаратор, Ситогидроциклонная установка,Илоотделитель,Пескоотделитель,Вакуумный дегазатор и т.д)
В последнее время компания KOSUN завершила проектирование, производство и изготовление системы контроля твердых фаз буровой установкемощностью 1000 л.с., которая готова к отправке в буровую компанию в Северной Африке для использования на строительной площадке. Эта система состоит из 4 резервуаров для бурового раствора, в керне используется вибросито, вакуумный дегазатор, пескоотделитель, илоотделитель и оборудование для четырехступенчатой очистки для удовлетворения технологических требований, связанных с циркуляцией бурового раствора, перфузией и обострением.
Система контроля твердой фазы на буровой установке мощностью 1000 л.с., производимая KOSUN, может выдерживать высокие температуры, взрывозащищенность, антикоррозионную защиту, защиту от дождя, маслостойкость (буровой раствор на масляной основе) и имеет соответствующую квалификацию конструкции и производства для деталей с особыми требованиями к взрывозащищенный и безопасный; он может не только обеспечить плавный ход подготовки бурового раствора, обострения, фильтрации, циркуляции, контроля и хранения и т. д., но также имеет сильную способность управления очисткой бурового раствора и твердой фазы. Подходит для автомобильных и железных дорог. перевозка на большие расстояния, может загружаться и разгружаться краном, а также транспортироваться на специальной тележке.
KOSUN специализируется на производстве оборудования для разделения твердой и жидкой фаз. Если у вас возникла необходимость вочистке бурового раствора, вы можете связаться с нами в любое время.
Эффективность работы трехступенчатой системы очистки буровых растворов определяется на первой ступени, когда используются вибросита. С помощью вибросита удаляется основная масса выбуренной породы и создаются условия для эффективной очистки на гидроциклонных установках. Известно, что наибольшая производительность вибросита в том случае, когда шлам состоит из песка, наименьшая, когда шлам представлен вязкими глинами. При бурении в глинистых отложениях закупорка ячеек частицами выбуренной породы приводит к большим потерям раствора.
Однако из практического опыта бурения нефтяных и газовых скважин на месторождениях Западной Сибири, Белоруссии известно, что из-за присутствия в верхнем интервале (300-800 м) геологического разреза пропластков вязких глин, переслаивающихся с песчанистыми отложениями, очистка раствора от выбуренной породы на виброситах неэффективна из-за постоянного прилипания частиц вязких глин к вибрирующей поверхности ситового полотна. Это приводит к закупорке ячеек сетки, уходу раствора в амбар и быстрому разрыву ситового полотна.
Во избежание потери значительного объема прокачиваемого раствора, циркуляции, приходится через приоткрытое отверстие в приемной емкости вибросита подавать неочищенный раствор, минуя сетки, в емкости циркуляционной системы. Это ведет к зашламлению приемных емкостей блока вибросит и гидроциклонов крупными частицами выбуренной породы, закупорку насадок гидроциклонов; снижение качества тонкой очистки буровых растворов и скорости бурения.
Очистка и регенерация бурового раствора — важный компонент циркуляционных систем буровых установок.
Обычно этот компонент представлен блоком очистки и регенерации бурового раствора, причем обработке подвергается так называемый утяжеленный буровой раствор
Утяжеленный буровой раствор — многокомпонентная полидисперсная система, в которой дисперсная фаза обычно представлена глиной, а дисперсионная среда — водой.
Установки очистки и регенерации бурового раствора главным образом предназначены для поддержания буровых работ с использованием малоотходных технологий и позволяют:
очищать буровые растворы от шлама с размером частиц более 5 мкм
(так, с помощью вибросита могут удаляться частицы более 65 микрон, ситогидроциклонная установка позволяет удалять частицы более 55 микрон, а пескоотделитель более 40 микрон и др.)
обрабатывать сливы песко- и илоотделителя на центрифуге
регенерировать барит (сульфат бария или тяжелый шпат) при бурении и после завершения бурения скважины
перерабатывать избытки бурового раствора, попутно разделяя его на фракции
дегазировать буровой раствор
В самом общем виде установки (блоки) очистки и регенерации бурового раствора комплектуются следующими субкомпонентами:
-линейный вибросит
-ситогидроциклонный сепаратор
-глиноотделить
-блок флокуляции
На буровых используются вакуумные дегазаторы. Величина разрежения регулируется в зависимости от структурно-механических свойств бурового раствора; под действием этого разрежения газированная жидкость поступает в одну из дегазационных камер.
Предпочтение необходимо отдавать вакуумным дегазаторам. Хлорная вода и водный раствор сернистого газа, образующиеся в газодозаторах, должны подаваться к месту их введения в обрабатываемую воду по резиновым шлангам, аммиачная вода и аммиак — по железным трубам. Смешение аммиака с водой должно производиться близ места его введения в обрабатываемую воду в особых смесительных колонках специальной конструкции.
Эффективность применения вакуумного дегазатора
Предлагаемое устройство относится к нефтяной и газовой промышленности и может быть использовано для дегазации буровых растворов при проводке нефтяных и газовых скважин.
Бесперебойная работа вакуумного дегазатора типа ДВС зависит от того, насколько правильно он подготовлен к работе. Перед пуском его следует проверить положение штока клапана-разрядника и при необходимости, переместить его вручную в крайнее положение; проверить вращение вала вакуумного насоса; заполнить выкидной отсек емкости буровым раствором так, чтобы выкидные клапаны погрузились в жидкость; подать воду в вакуумный насос.
На блоке установлены вакуумный дегазатор, механические и гидравлические перемешиватели.
В США распространен вакуумный дегазатор с двумя камерами. Он выполнен в виде цилиндрического горизонтального корпуса, на котором установлены 203-мм труба для принятия газированного раствора и вакуумный насос. Величина разрежения 0 02 — 0 04 МПа в зависимости от плотности раствора. Раствор поступает в цилиндрический корпус и, полностью заполняя его, растекается по веей длине трубы на отбойные пластины.
В настоящее время вакуумные дегазаторы применяются во всех газонефтедобывающих районах Советского Союза с различными геолого-техническими условиями бурения скважин.
Необходимость решения задач по переработке буровых отходов параллельно с процессом бурения ствола скважины уже давно стоит в повестке дня всех буровых компаний и по мере ужесточения экологических требований со стороны государственных служб актуальность проблемы будет неуклонно возрастать.
Буровой шлам – общее понятие, относящееся к выбуренной породе, смоченной буровым раствором, а также смесь выбуренной породы с технологическими жидкостями и буровым раствором, применяемыми при строительстве скважины.
Технологические отходы бурения – в первую очередь, это буферные жидкости, используемые в процессе тампонажных работ и часть тампонажного раствора в смеси с буровым раствором. При освоении скважины часто применяют технологические жидкости на основе водных растворов хлористого калия, натрия и кальция. В аварийных ситуациях возможно применение кислот и других технологических жидкостей.
Для утилизации нефтяных шламов считается важным факт расслоения продуктов на такие весьма условные виды отходов:
Как ни странно, но утилизация нефтесодержащих отходов сегодня напоминает методы далекого средневековья и, несмотря, на существование современного оборудования, все еще находят место такие способы:
Отстаивание, основными недостатками которого считаются длительность, необходимость привлечения больших площадей, а также применение немалых доз химикатов, влияющих на расслаивание.
Фильтрация. Недостатки этого метода, прежде всего в том, что объемы накапливающихся нефтешлаков значительно превышают пропускную способность существующего очистного оборудования. Это мешает провести финальную утилизацию, уже отфильтрованного материала, остается нерешенной проблема отделения воды.
Сжигание. Нетрудно догадаться, что это экономически не выгодный способ утилизации нефтепродуктов. Сжигаемые углеводороды, не просто загрязняют окружающую атмосферу, но также лишают предпринимателя шансов использовать ценный материал еще раз.